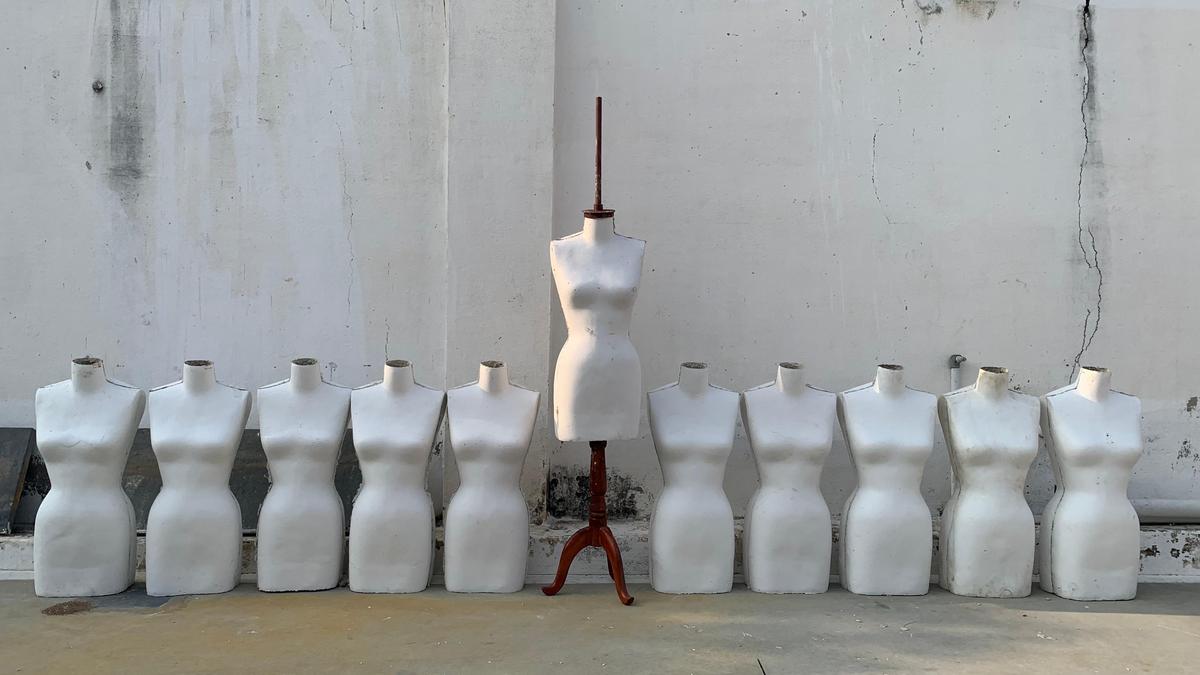
Joothi Special Papers Turn Cotton Scraps into Biodegradable Manquins
Further days ago, Aerod-based Joothy Specialty Papers is a video that highlights his project on Instagram, highlighting the biodgrade Manquins-Wint viral. If you are wondering how this project has come, the brand has a backstory here.
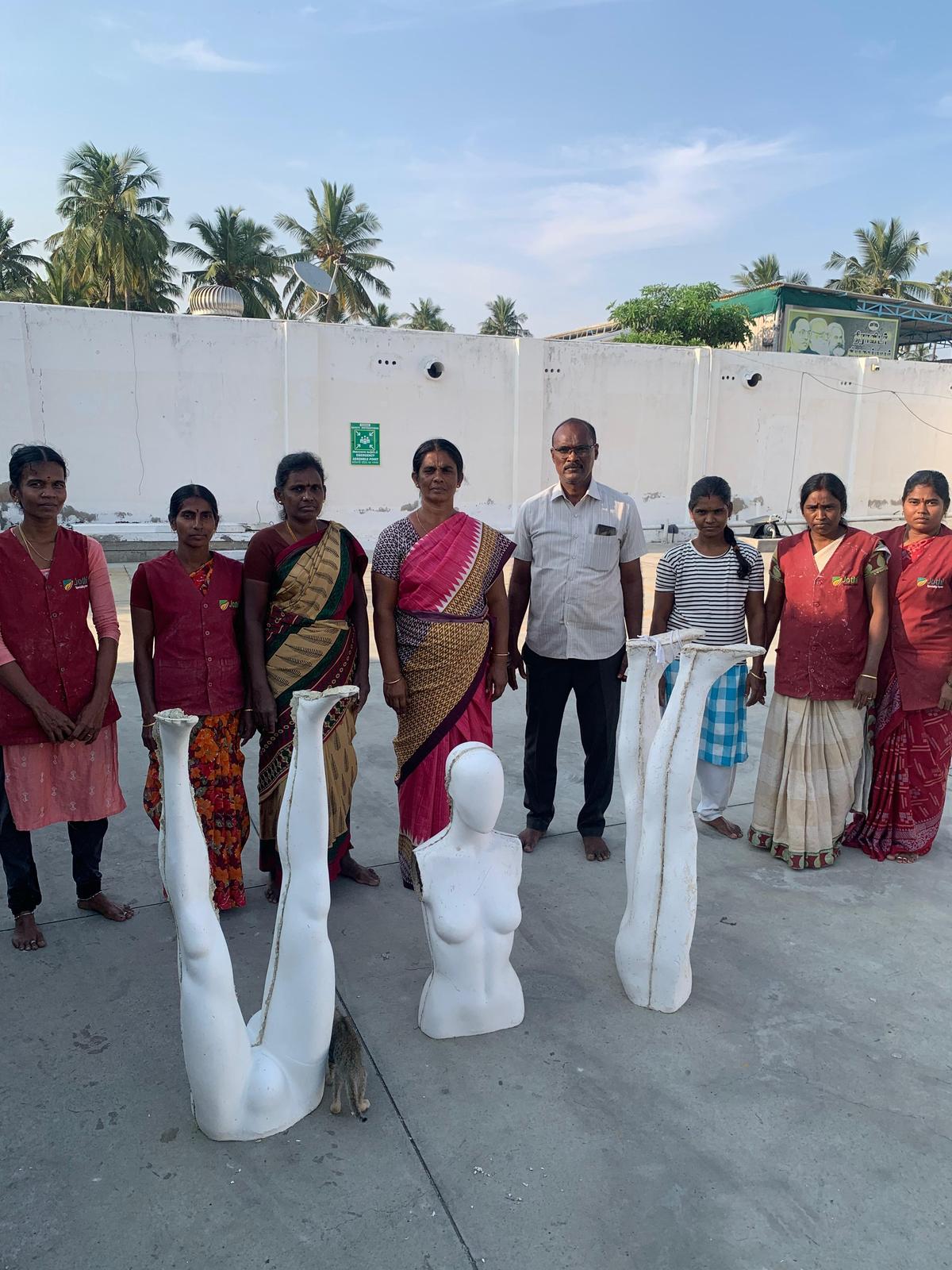
Mani P (Center) and his wife (fourth to the left) with the team Photo Credit: Special Arrangement
Mani P and his wife, the company has been producing recycling cotton rag paper from textile scraps since 1996. Upon rising in the landfills, it was realized that there were several other reasons for settling extra fabric waste. We have decided to convert this waste fabric into recycling cotton paper. We also wanted to make sure they were used in the same textile factory for their packing, price tag, etc.
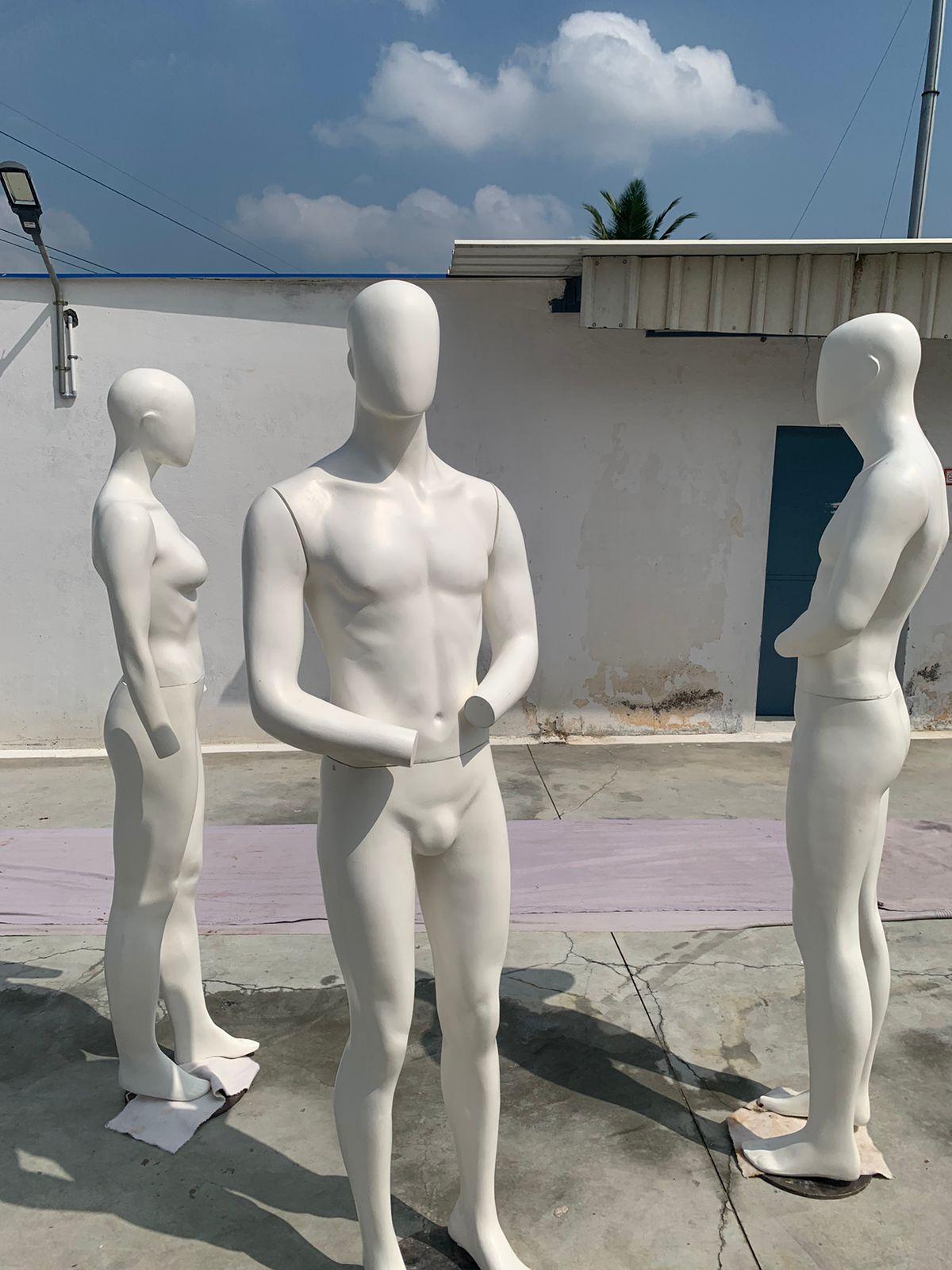
The process of craftsmanship begins with brand sourcing fabric waste from the garment factories in this region. Photo Credit: Special Arrangement
Call for change
On the 21st, the jewelry brand Tanishik was contacted with a unique request to Mani and his team. They sought the buses of environmentally-friendly jewelry to replace their existing plastic or fiber parts. “We have studied for one year to create these display stands from the Scrap Cotton Fabric,” Mani said, who regularly supplies handmade paper to Bengaluru, which takes the call of the jewelry brand.
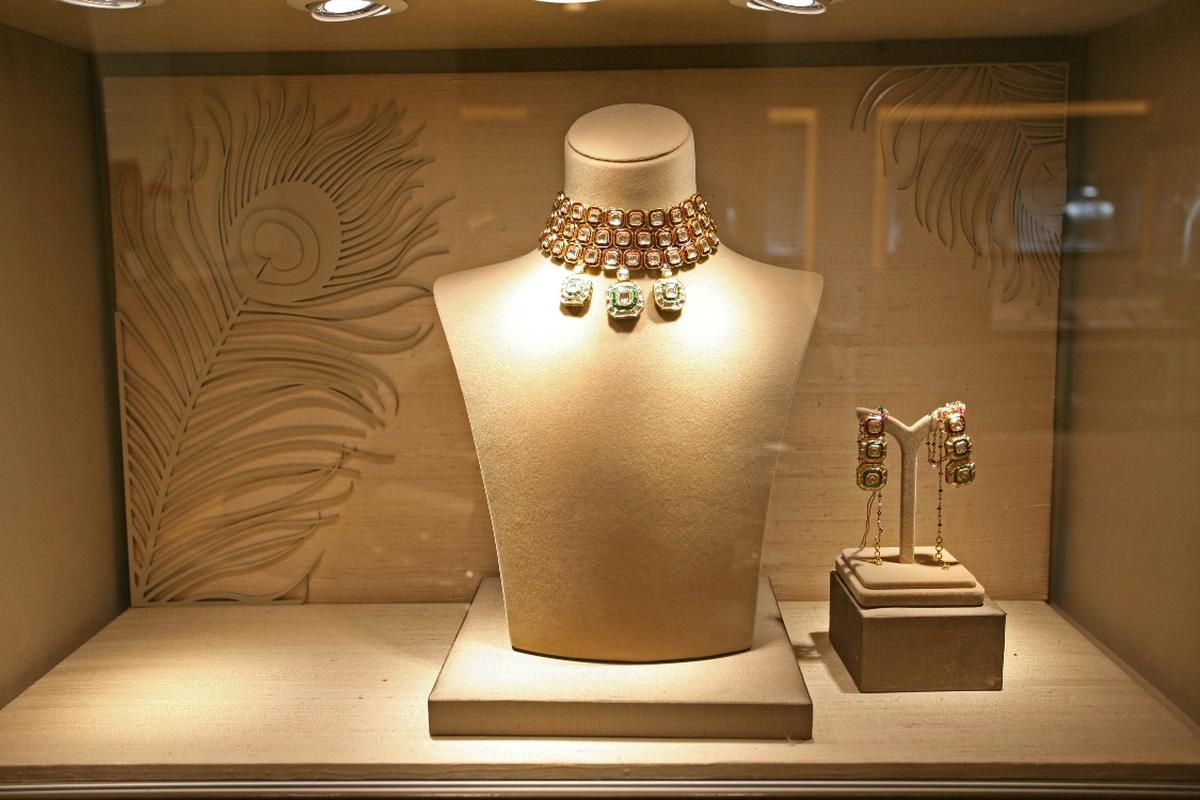
Tanishok 20,000 Manquine sources annually for their 500 outlets across India | Photo Credit: Special Arrangement
Ayil Raghavan, a senior manager of the Titan Company’s jewelry department, said the collector came when they started handmade paper sourcing from Mani for the company. “After visiting them and studying their process, I have decided to test Eco Manquins with Titan’s deputy group manager Ajay Kumar Bibi and developed them today, we have developed them today, 20,000 outlets of Tanisak for Tanisak’s 500 outlets across India. Source of the standard.
After providing these stands for more than a decade, Mani and his team wanted to do more to solve plastic waste in the industry. “In 2023, we heard that ‘Manquin Gravelliards’ is discarded where used statues are discarded.
It takes two people a week to make an idol Photo Credit: Special Arrangement
The process of doing a standard craft with brand sourcing fabric waste from the garment factories in this region begins. “The rest of the cotton fabric is collected by us and decoration from the making of clothing, toys, mats, etc. This decoration is a natural and biodgradable adhesive, molding, etc. to craft a 30-shift manquinnus with a mixture of decoration, “the gem explains. Each statue is handicapped by a All-governance and it takes two people to make it a week to make it.” They are naturally dialed because using machines can damage their form and this process takes two to three days ”
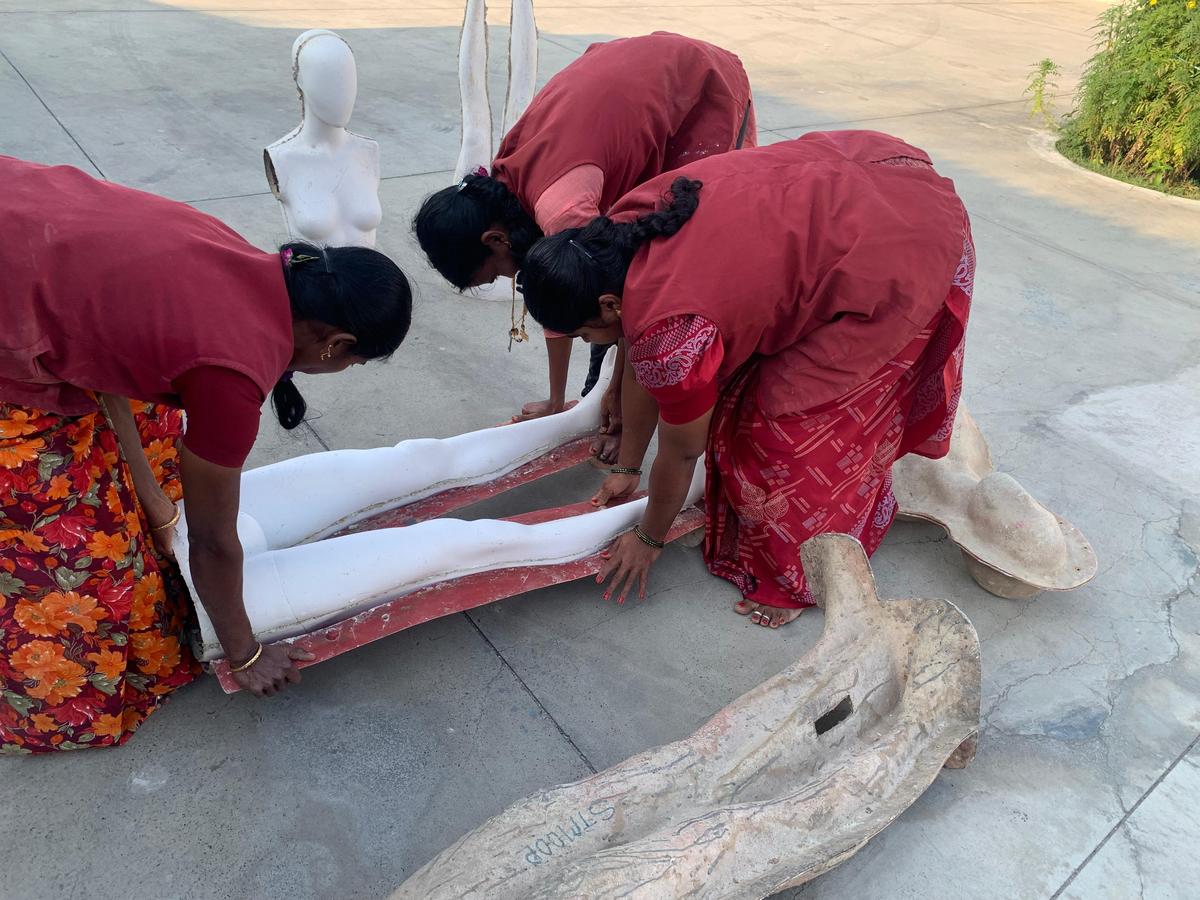
Each of each statue is handicrafts by a single team Photo Credit: Special Arrangement
100 T-shirt = 1 Mankin
Taking it through our process, “Each standard can last up to five years and if used nearby, it can last for two to three years,” Mani says their prices depend on the sagg between 5,000 and 25,000. “We recycled on 100 T-shirts (25-35 kg textile fabric waste) to make a standard. They are 20% light, anti-bacterial and anti-fungal and customized in the weight than plastic/fiber variants. Eyl That they used fiber manquin “echo variants light-wiite. Although they are expensive and need to be changed every few years, their environmental facilities surpass these concerns. “
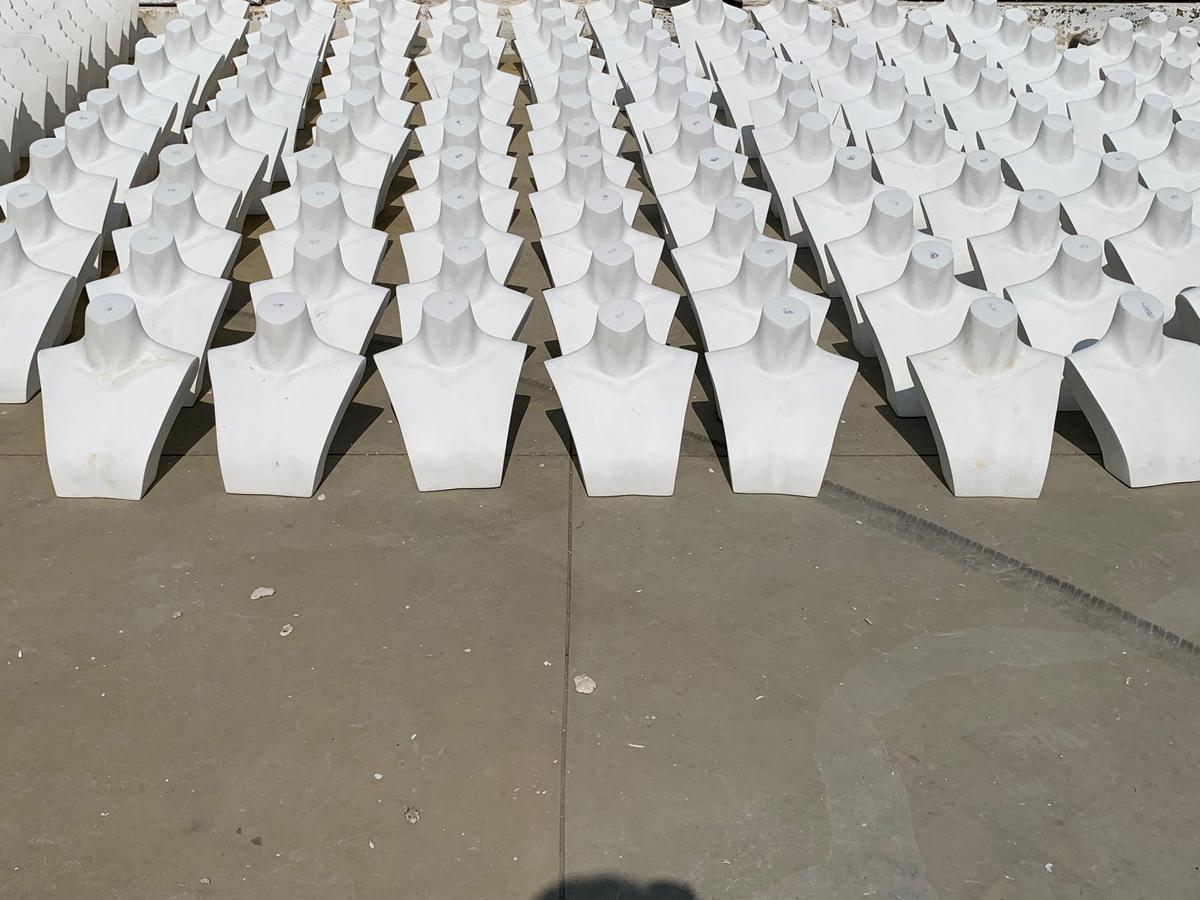
Dry process | Photo Credit: Special Arrangement
These statues can be biodgrade in two ways: put them on the ground slowly for degradation, or break them into their pies,. “The ex-biodegradation method takes two to three months and subsequently takes about two to three weeks based on the climate. Warm temperatures lead to rapid degradation and if companies do not want to use the soil method we can also send them to recycling facilles,”. Money explained.
100 T-shirt (25-35 kg textile fabric waste) is used to create a standard. Photo Credit: Special Arrangement
After saying this, why do these values still react to other brands? The gem explains that time and effort that goes to them, is needed to work with the team “high fragment”. “The orders are not possible,” said Mani, who is now searching from textile brands abroad.
Published – Feb 05, 2025 11:26 AM IST